Leading Tips for Selecting Reliable Distributors of High-Quality Chemical Products
Leading Tips for Selecting Reliable Distributors of High-Quality Chemical Products
Blog Article
Secret Considerations for Selecting the Right Chemical Products to Accomplish Effective Integrated Solutions in Your Operations
Choosing the ideal chemical products for incorporated services in operations needs a complex approach that encompasses various vital factors to consider. From analyzing chemical compatibility to guaranteeing adherence to regulative requirements, each aspect plays an essential function in enhancing operational efficiency and safety.
Recognizing Chemical Compatibility
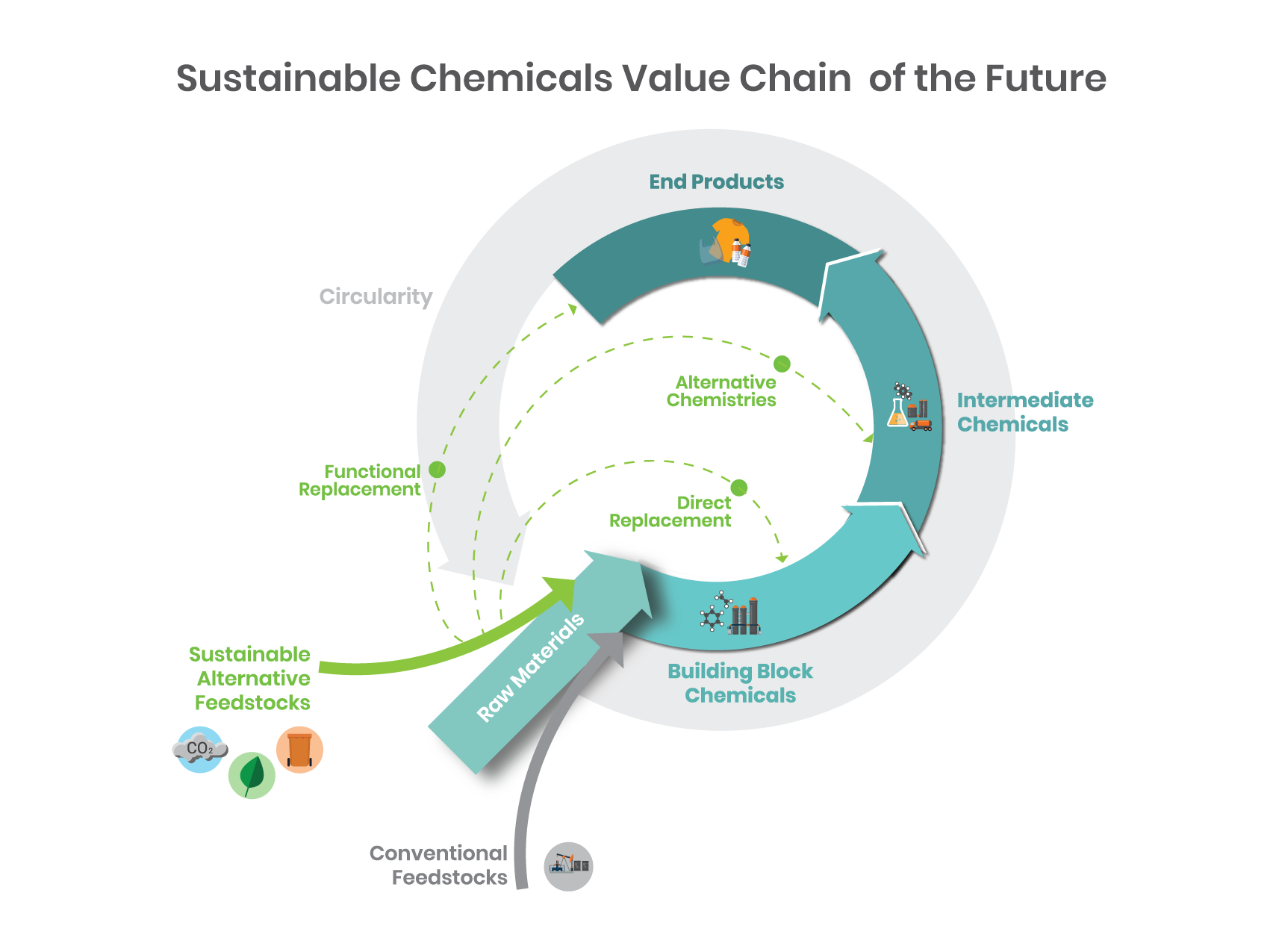
To assess compatibility, one need to think about factors such as the chemical residential or commercial properties of the materials entailed, including pH, focus, temperature, and the existence of contaminations. Using compatibility graphes and data sources can offer beneficial insights into possible communications. Additionally, carrying out small examinations can help determine unanticipated responses that might not be recorded.
Factors such as moisture, light exposure, and temperature can affect the security and reactivity of chemical items. By prioritizing chemical compatibility throughout the choice process, companies can improve functional effectiveness, decrease the threat of mishaps, and ensure conformity with safety methods.
Assessing Governing Compliance
In the facility landscape of chemical product option, examining regulatory compliance is extremely important to guaranteeing not just safety yet also legal adherence. Organizations has to navigate a myriad of policies, from neighborhood and national legislations to global criteria, that govern the use, storage space, and disposal of chemical materials. This calls for a detailed understanding of relevant guidelines such as the Occupational Safety and Wellness Administration (OSHA) criteria, the Environmental Protection Agency (EPA) guidelines, and the European Union's Registration, Examination, Authorisation and Constraint of Chemicals (REACH)
When picking chemical items, it is necessary to confirm that providers supply Safety and security Information Sheets (SDS) that information prospective risks and managing demands. Services should validate that the chemicals conform with industry-specific policies, which might enforce additional specifications. Non-compliance can bring about serious charges, consisting of fines and operational closures.
Additionally, companies ought to remain updated on governing modifications, as non-compliance can occur from obsolete practices. Creating a robust conformity technique, consisting of regular audits and staff member training, can help make sure adherence to current guidelines. Ultimately, prioritizing governing compliance not just mitigates danger yet also improves the company's reputation and operational performance.
Assessing Environmental Influence
How can companies properly analyze the environmental impact of chemical products during the choice process? A thorough assessment needs a diverse strategy, including information on the life process of items, from manufacturing to disposal. Organizations needs to start by recognizing the possible threats connected with each chemical, consisting of poisoning, perseverance in the atmosphere, and bioaccumulation potential. Utilizing devices such as Safety and security Information Sheets (SDS) and ecological danger evaluations makes it possible for a more clear understanding of these elements.
Furthermore, companies can take official site advantage of third-party qualifications and eco-labels that indicate compliance with environmental standards - Chemical Products. Involving with providers that prioritize sustainability methods can likewise improve the choice procedure. It is crucial to analyze not just the direct effects of chemical usage but also the indirect influences, such as energy consumption and waste generation
Executing life cycle assessment (LCA) methods can give detailed insights into the ecological impact of chemical items, highlighting locations for enhancement. By focusing on openness and cooperation with stakeholders, organizations can make informed choices that line up with their sustainability goals while minimizing adverse environmental outcomes. This aggressive technique eventually promotes a much more responsible and eco-conscious functional framework.
Evaluating Cost-Effectiveness
While reviewing chemical items for functional usage, organizations should additionally take into consideration cost-effectiveness as a crucial consider the option procedure. This entails evaluating not only the first purchase price yet also the overall expense of possession, which includes aspects such as use performance, maintenance, and disposal costs. Chemical Products. An item that appears economical upfront may incur higher expenses in power intake or call for more regular replacement, inevitably affecting the lower line
Additionally, companies ought to evaluate the capacity for cost financial savings via maximized formulations that enhance performance and minimize waste. For instance, items that need reduced application rates or provide faster processing times can result in substantial financial savings with time. It is likewise important to take into consideration the influence of regulatory conformity costs, as non-compliance can cause fines and enhanced operational costs.
Furthermore, companies must evaluate the lasting value derived from the chemical items, including boosted high quality, increased performance, and improved security. A detailed cost-effectiveness analysis empowers companies to make educated choices that line up with both their economic goals and other functional purposes, inevitably resulting in lasting and effective practices.
Identifying Provider Integrity
Provider integrity is critical when picking chemical products for procedures, as it directly influences both product high quality and functional efficiency. A reliable provider constantly supplies top quality items promptly, making certain that your processes continue to be uninterrupted. To identify provider dependability, begin by examining their track record within the sector. Choose reviews, testimonies, and instance researches that highlight their efficiency and consumer satisfaction degrees.
Next, my blog take into consideration the supplier's background of compliance with guidelines and standards. A trustworthy distributor must have a durable quality control program that follows industry guidelines. In addition, evaluate their ability to offer technical assistance and product info, which is vital for notified decision-making.

Verdict
In conclusion, picking the suitable chemical products for integrated solutions demands an extensive analysis of several important variables. Recognizing chemical compatibility, making sure governing conformity, assessing environmental effects, analyzing cost-effectiveness, and recognizing reputable providers collectively contribute to educated decision-making.
Report this page